E-Catalog > VEKTEK USA > Metric TuffCam Swing Clamps
Product Information :
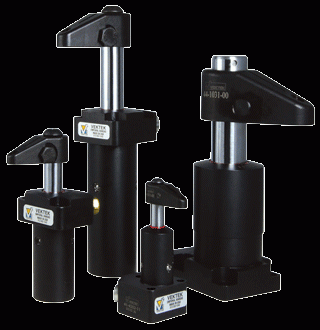
- เครื่องจักร, อุปกรณ์เกี่ยวกับเครื่องจักร, เครื่องมือกล
- VEKTEK USA
- สินค้า, ผลิตภัณฑ์
Product Detail :
Metric TuffCam™ Swing Clamps
TuffCam™ Swing Clamps meet your demand for a product that can handle the stress and positioning requirements of high-speed or heavy arm applications. These tri-cam design clamps, with their patented Cam Follower Seat, can position and clamp in one second or less, handle large arms with ease and include the Clockingfeature that dramatically reduces the time it takes to change arms for maintenance, replacement or fixture setup. Available in these body styles:
|
U. S. Patent Nos. |
TuffCam™ Top Flange Swing Clamps
Specifications
![]() U.S. Patent No. 5,820,118 |
![]() |
|||||||||||||||||||||||||||||||||||||||||||||||||||||||||||||||||||||||||||||||||||||||||||||||||||||||||||||||||
|
All dimensions are in mm. Warning! Never allow swing arm to contact workpiece or fixture during arm rotation ** Cylinder capacities are listed at 350 bar (35 MPa) maximum operating pressure, with a standard length VektorFlo® arm installed. Minimum operating pressure is 52 bar (5,2 MPa) for single acting, 35 bar (3,5 MPa) for double acting. The clamping force is adjustable by varying the hydraulic system pressure. To determine the approximate output force for your application, divide the cylinder capacity shown above by 350, and multiply the resultant number X your system operating pressure to obtain the approximate clamping force for your application. (Actual force will vary slightly due to internal cantilever loading, friction loss and/or return springs.) *** To allow for work piece height variations, it is recommended that the vertical travel be set to about 50% of the vertical stroke. **** To insure maximum service life and trouble-free operation, restrict fluid flow to the level indicated in the Clamp Time and Flow Rate Chart. Order Arms separately
|
TuffCam™ Top Flange Long Stroke
Specifications
Double Acting |
|
||||||||||||||||||||||||||||||||||||||||||||||||||||||||||||||||||||||||||||||||||
|
|||||||||||||||||||||||||||||||||||||||||||||||||||||||||||||||||||||||||||||||||||
Warning Never allow swing arm to contact workpiece or fixture during arm rotationor Standard Swing Clamp models. Check overall dimensions for correct * Cylinder capacities are listed at 3 50 bar (35MPa)maximum operating pressure, with a standard length Vektorflo® arm installed. Minimum operating pressure is 500 psi for double acting. The clamping force is adjustable by varying the hydraulic system pressure. To determine the approximate output force for your application, divide the cylinder capacity shown above by 350, and multiply the resultant number X your system operating pressure to obtain the approximate clamping force for your application. (Actual force will vary slightly due to internal cantilever loading and friction loss.) ** To allow for work piece height variations, it is recommended that the vertical travel be set to about 50% of the vertical stroke. *** To ensure maximum service life and trouble-free operation, restrict fluid flow per table. |
![]() |
||||||||||||||||||||||||||||||||||||||||||||||||||||||||||||||||||||||||||||||||||
TuffCam™ Bottom Flange Swing Clamps
Specifications
Double and Single Acting |
|
|||||||||||||||||||||||||||||||||||||||||||||||||||||||||||||||||||||||||||||||||||||||||||||||||
|
||||||||||||||||||||||||||||||||||||||||||||||||||||||||||||||||||||||||||||||||||||||||||||||||||
All dimensions are in mm. Warning! Never allow swing arm to contact workpiece or fixture during arm rotation. ** Cylinder capacities are listed at 350b bar (35 MPa) maximum operating pressure, with a standard length Vektorflo® arm installed. Minimum operating pressure is 52 bar (5,2 MPa) for single acting, 35 bar (3,5 MPa)for double acting. The clamping force is adjustable by varying the hydraulic system pressure. To determine the approximate output force for your application, divide the cylinder capacity shown above by 350 and multiply the resultant number X your system operating pressure to obtain the approximate clamping force for your application. (Actual force will vary slightly due to internal cantilever loading, friction loss and/or return springs.) *** To allow for work piece height variations, it is recommended that the vertical travel be set to about 50% of the vertical stroke. **** To insure maximum service life and trouble-free operation, restrict fluid flow to the level indicated in the Clamp Time and Flow Rate Chart. |
TuffCam™ Bottom Flange Long Stroke Swing Clamps
Specifications
|
|
||||||||||||||||||||||||||||||||||||||||||||||||||
|
|||||||||||||||||||||||||||||||||||||||||||||||||||
Warning! Never allow swing arm to contact workpiece or fixture during arm rotation. ** Cylinder capacities are listed at 350 bar (35 MPa) maximum operating pressure, with a standard length Vektorflo® arm installed. Minimum operating pressure is 52 bar (5,2 MPa) for single acting, 35 bar (3,5 MPa)for double acting. The clamping force is adjustable by varying the hydraulic system pressure. To determine the approximate output force for your application, divide the cylinder capacity shown above by 350 and multiply the resultant number X your system operating pressure to obtain the approximate clamping force for your application. (Actual force will vary slightly due to internal cantilever loading, friction loss and/or return springs.) *** To allow for work piece height variations, it is recommended that the vertical travel be set to about 50% of the vertical stroke. **** To insure maximum service life and trouble-free operation, restrict fluid flow to the level indicated in the Clamp Time and Flow Rate Chart. |
![]() |
||||||||||||||||||||||||||||||||||||||||||||||||||
All dimensions are in mm. Warning! Never allow swing arm to contact workpiece or fixture during arm rotation. ** Cylinder capacities are listed at 350 bar (35 MPa) maximum operating pressure, with a standard length Vektorflo® arm installed. Minimum operating pressure is 52 bar (5,2 MPa) for single acting, 35 bar (3,5 MPA)for double acting. The clamping force is adjustable by varying the hydraulic system pressure. To determine the approximate output force for your application, divide the cylinder capacity shown above by 350 and multiply the resultant number X your system operating pressure to obtain the approximate clamping force for your application. (Actual force will vary slightly due to internal cantilever loading, friction loss and/or return springs.) *** To allow for work piece height variations, it is recommended that the vertical travel be set to about 50% of the vertical stroke. **** To insure maximum service life and trouble-free operation, restrict fluid flow to the level indicated in theClamp Time and Flow Rate Chart. |
Metric TuffCam™ Low Profile Top Flange Swing Clamps
![]() |
|
||||||||||||||||||||||||||||||||||||||||||||||||||||||||||||||||||||||||||||||||||||||||||||||||||||||||||||||||||||||||||||||||||||||||||||||||||||||||||||||||
WARNING: Never allow swing arm to contact workpiece or fixture during rotation. Cylinder capacities are listed at 350 bar (35 MPa) maximum operating pressure with a standard VektorFlo® arm installed. See the Arm Length and Pressure Limitations graph for clamping force with various other arm lengths installed. The clamping force is adjustable by varying the hydraulic system pressure. To determine the approximate output force for your application, divide the cylinder capacity from the graph by 350 (35 MPa), and multiply the Resultant Number times Your System Operating Pressure to obtain the approximate clamping force for your application. Actual force will vary slightly due to internal cantilever loading, friction loss and/or return springs. ** To allow for piece part height variations, it is recommended that the vertical travel be set at about 50% of the vertical stroke. *** To insure maximum service life and trouble-free operation, restrict fluid flow to the level indicated in the Clamp Time and Fluid Flow Rate chart. |
|||||||||||||||||||||||||||||||||||||||||||||||||||||||||||||||||||||||||||||||||||||||||||||||||||||||||||||||||||||||||||||||||||||||||||||||||||||||||||||||||
WARNING: Never allow swing arm to contact workpiece or fixture during rotation. Cylinder capacities are listed at 350 bar (35 MPa) maximum operating pressure with a standard VektorFlo®arm installed. See the Arm Length and Pressure Limitations graph for clamping force with various other arm lengths installed. The clamping force is adjustable by varying the hydraulic system pressure. To determine the approximate output force for your application, divide the cylinder capacity from the graph by 350 (35 MPa), and multiply the Resultant Number times Your System Operating Pressure to obtain the approximate clamping force for your application. Actual force will vary slightly due to internal cantilever loading, friction loss and/or return springs. ** To allow for piece part height variations, it is recommended that the vertical travel be set at about 50% of the vertical stroke. *** To insure maximum service life and trouble-free operation, restrict fluid flow to the level indicated in theClamp Time and Fluid Flow Rate chart. |
![]() |
Metric TuffCam™ Low Profile Bottom Flange Swing Clamps
Specifications
|
![]() |
|||||||||||||||||||||||||||||||||||||||||||||||||||||||||||||||||||||||||||||||||||||||||||||||||||||||||||||||||||||||||
|
||||||||||||||||||||||||||||||||||||||||||||||||||||||||||||||||||||||||||||||||||||||||||||||||||||||||||||||||||||||||||
WARNING: Never allow swing arm to contact workpiece or fixture during rotation.
Cylinder capacities are listed at 350 bar (35 MPa) maximum operating pressure with a standard VektorFlo® arm installed. See the Arm Length and Pressure Limitations graph for clamping force with various other arm lengths installed. The clamping force is adjustable by varying the hydraulic system pressure. To determine the approximate output force for your application, divide the cylinder capacity from the graph by 350 (35 MPa), and multiply the Resultant Number times Your System Operating Pressure to obtain the approximate clamping force for your application. Actual force will vary slightly due to internal cantilever loading, friction loss and/or return springs. ** To allow for piece part height variations, it is recommended that the vertical travel be set at about 50% of the vertical stroke. *** To insure maximum service life and trouble-free operation, restrict fluid flow to the level indicated in theClamp Time and Fluid Flow Rate chart. |
![]() |
|||||||||||||||||||||||||||||||||||||||||||||||||||||||||||||||||||||||||||||||||||||||||||||||||||||||||||||||||||||||||
Metric TuffCam™ Rod Position Sensing Swing Clamp
![]() |
|
||||||||||||||||||||||||||||||||||||||||||||||||||||||||||||||||
These systems available as Double Acting All dimensions are in inches. |
etric Magnetic Position Sensing Swing Clamps
Sensor Kits Ordered Separately
The use of NPN or PNP is determined by the type of control unit to which the sensor is connected. One Sensor is required for each sensing position. Sensor Features
|
|
|||||||||||||||||||||||||||||||||||||||||||||||||||||||||||||||
Refer to non-position sensing TuffCam™ Low Profile Swing clamps for full Dimension information. These systems available as Double Acting All dimensions are in mm |
81-5505-45
81-5505-60
81-5518-60
81-5518-45
81-5513-60
81-5513-45
81-5509-60
81-5509-45
81-5513-30
81-5505-30
81-5509-30
81-5518-30
41-5222-11
41-5222-12
41-5222-21
41-5222-22
41-5222-10
41-5222-20
41-5233-11
41-5233-12
41-5233-10
41-5233-21
41-5233-22
41-5233-20
41-5622-11
41-5622-12
41-5622-21
41-5622-23
41-5622-22
41-5622-24
41-5633-11
41-5622-10
41-5622-20
41-5633-12
41-5633-10
41-5633-21
41-5633-23
41-5633-22
41-5633-24
41-5633-20
81-5519-30
81-5519-45
81-5519-60
81-5522-30
81-5522-45
62-1401-11
62-1401-02
62-1401-04
62-1401-05
62-1401-07
62-1401-12
62-1401-15
62-1401-01
62-1401-03
62-1401-06
62-1401-08
62-1401-09
62-1401-10
62-1401-13
62-1401-14
62-1401-16
30-8711-20
47-0203-71
47-0203-74
41-4602-11
41-4602-22
41-4605-21
41-4611-11
41-4611-12
41-4611-21
41-4602-12
41-4602-21
41-4605-11
41-4605-12
41-4611-22
41-4605-22
47-0203-71
47-0203-74
41-4605-24
41-4611-24
41-4605-23
41-4611-23
47-0203-71
47-0203-74
41-4211-12
41-4202-11
41-4202-22
41-4205-11
41-4205-12
41-4205-22
41-4211-11
41-4211-21
41-4202-12
41-4202-21
41-4205-21
41-4211-22
47-0203-71
47-0203-74
41-4211-23
41-4205-23
41-4211-24
41-4205-24
47-0203-74
41-4622-11
41-4622-12
41-4622-15
41-4622-21
41-4622-22
41-4622-23
41-4622-24
41-4622-25
41-4633-11
41-4633-12
41-4633-21
41-4633-22
41-4633-25
41-4633-23
41-4633-24
41-4633-15
47-0203-74
41-4222-11
41-4222-12
41-4222-15
41-4233-11
41-4233-21
41-4222-21
41-4222-22
41-4222-25
41-4233-12
41-4233-15
41-4233-22
41-4233-25
47-0203-74
41-4233-21-PR
41-4233-22-PR
41-4622-21-PR
41-4622-22-PR
41-4633-23-PR
41-4633-25-PR
41-4222-21-PR
41-4233-25-PR
41-4622-23-PR
41-4622-24-PR
41-4622-25-PR
41-4633-21-PR
41-4633-22-PR
41-4633-24-PR
29-7001-00
27-6424-00
29-7001-01
47-0203-74
41-4222-21-PS
41-4222-22-PS
41-4233-25-PS
41-4622-21-PS
41-4622-25-PS
41-4633-21-PS
41-4222-25-PS
41-4233-21-PS
41-4233-22-PS
41-4622-22-PS
41-4622-23-PS
41-4633-22-PS
41-4633-23-PS