E-Catalog > TAC Rockford for machine Tools > ForceCheck
Product Information :
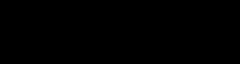
- เครื่องจักร, อุปกรณ์เกี่ยวกับเครื่องจักร, เครื่องมือกล
- TAC Rockford for machine Tools
- สินค้า, ผลิตภัณฑ์
Product Detail :
Why Check Drawbar Force?
Is your power drawbar working correctly?
Improve tool life and part finish
Correct tool holding force ensures that the spindle-tool holder interface is as rigid as possible. A rigid interface will improve tool life by reducing chatter and excess wear, and in turn improve workpiece finish.
Protect your spindles and ensure machining accuracy
Insufficient tool holding force can quickly wear or damage the critical spindle taper resulting in loss of machine accuracy and an expensive repair bill.
For the HSK taper, wear and damage on the spindle taper are even more detrimental. The HSK taper relies on an interference fit between the spindle and tool holder tapers, meaning drawbar force must be sufficient for the tool holder to properly seat. Because the HSK interface seats both on the tool holder taper and flange, dimensional tolerances are extremely tight. For HSK forms E and F, correct clamping force is crucial because there are not drive keys or dogs to transmit torque–the system relies entirely on the power drawbar's holding force.
Predict problems with the spindle's Belleville / disk spring stack
Machining centers with automatic tool clamping systems typically use Belleville/disk spring stack to hold a tool in the spindle, with a hydraulic cylinder used to overcome the spring force to unclamp the tool.
High RPM is often an important design criterion for a spindle, meaning the use of small diameter bearings makes sense from an engineering standpoint. Small bearings necessitate the use of small diameter springs to fit into the spindle arbor. Small-diameter springs lead to highly stressed springs for tool clamping, and even more so during tool unclamp.
A typical drawbar spring stack is designed to last approximately 1 million cycles. This may sound like a big number, but tool changes add up quickly. An example: a process with 3 to 4 tool changes per minute (many do much more), with 2,000 operating hours per year (one shift), means between 360,000 and 480,000 cycles are made per year. In this scenario, the springs have reached the end of the design life cycle and should be replaced after two years. We have found some processes that reach 1 million cycles after 6 months–with the complaint that the "springs break all the time."
Springs will not break all at once. Initially only one spring might break without significant impact on tool holding force. However, soon others will break since they have to do the work of the broken spring (or springs) as well. The rest of the springs will be overloaded and break or take a permanent set.
This failure process can be detected with a clamping force measuring device and action be taken before the clamping system fails completely.
Check for the role that friction plays in the clamping system and for proper lubrication
Some drawbar designs use a mechanical force intensification mechanism to increase tool holding force. When force intensification is used, friction is a factor to be watched. It is difficult to quantify friction without measurement. Machine builders typically provide a tool holding force specification for properly lubricated and adjusted clamping system.
Most power drawbar systems with HSK tapers use force intensification in the gripper design. The mechanical intensification of the force is typically between 3 and 9 times, making friction a major factor in the proper operation of the system.
For systems with manual HSK grippers such as those supplied by Mapal and Guehring, periodic verification of correct tool holding force is also of critical importance. Per manufacturer recommendation, tools should be clamped using a torque wrench to ensure correct force. However, if the gripper is not properly lubricated, tool holding force will be much lower at the specified torque.
Operator safety
Eventually, the tool holding system of a machine will fail catastrophically if left unchecked. There will be lots of mysterious problems such as poor part finish and broken tools, and eventually leading to the tool flying out of the spindle and damaging the workpiece, machine, or worse–injuring the operator.
Standards compliance
- The ISO and DIN HSK standards have recommended minimum clamping forces. The ForceCheck gauge can verify that these are met.
- The "CAT" steep taper standard ASME B5.50 specifically recommends using a drawbar force gauge.
- ISO 9000 compliance requires that critical machine parameters be periodically checked.
HSK Taper
Measuring bars, complete sets, and base sets for all HSK type spindles. Contact us for other wireless and carrying case options.
Steep Taper (SK-DIN)
Measuring bars, complete sets, and base sets for Steep Taper (SK) DIN standard. Metric or inch retention knob / pull-stud threading available on each measuring bar.
Steep Taper (CAT/ANSI)
Measuring bars, complete sets, and base sets for Steep Taper (SK) CAT-ANSI. Metric or inch retention knob / pull-stud threading available on each measuring bar.
Steep Taper (ISO)
Measuring bars, complete sets, and base units for measuring drawbar force on a Steep Taper (SK) ISO standard spindle.
PSK Capto
Measuring bars, complete sets, and base units for measuring drawbar force on Coromant Capto spindles (Polygonal Shank Taper - PSK).
ForceCheck Turning-Center Chuck Force Gauges
Turning-center force sensors are designed to measure the holding force of clamp jaws on chucks. This allows manufacturers to make critical adjustments, and improve repeatability and workpiece quality. The wireless version of the chuck force gauge is able to measure RPM along with force.
For more advanced features, such as graphing and testing multiple machines as part of a preventive maintenance plan, a tablet that universally connects to any ForceCheck sensor is also available. Contact us for more specifications and details on advanced machine force measuring.
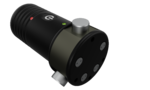
Wireless Chuck Force Gauges
The ForceCheck wireless chuck force gauge is designed to quickly and accurately measure holding force and speed on chucks. Verifying chuck holding force allows manufacturers to improve the repeatability of a manufacturing process by checking actual holding force under dynamic (rotating) conditions, as well as perform critical preventative maintenance checks. Contact us for other clamping diameters and extension rings, as well as 4+ jaw chucks. Details
PDF (495.320)
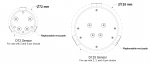
Wired Chuck Force Gauges
Designed to quickly check the holding force on a chuck or turning-center. The wired chuck force gauge can be customized for any diameter. Details
PDF (495.205)
ForceCheck Collet Force Gauges
With the ForceCheck collet force gauge, the clamping forces on collets and hydraulic tool holders can be measured to obtain accurate machining specifications while fulfilling ISO standard requirements. Available in complete sets for 1/4, 1/2, 3/4, 1, 10 mm, 16 mm, 20 mm, 25 mm and other diameters.
The ForceCheck collet force gauge allows tool holder and workholding collet holding force to be quickly and easily measured.
Because it is problematic to measure, this critical holding force is typically not checked, even though it plays an important role in manufacturing repeatability.
TAC Rockford, makers of the ForceCheck drawbar clamping measurement system, offers a simple, efficient, and consistently accurate collet force measurement unit.
With this system you can accurately and consistently measure the clamping forces on collets and hydraulic tool holders to obtain accurate machining specifications while fulfilling your company's or customer's ISO standard requirements.
Complete sets include a durable display with standard 9 volt battery, connecting cable, carrying case, and measuring bar.
Individual measuring bars for any size diameter are available.
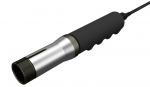
Application Example
Workholding 5C Collet Drawbar Force Gauge
ForceCheck collet force gauges measure the drawbar pullback force of a collet workholding system. Measurement of collet drawbar force provides an easy way to ensure correct force from machine to machine, or between setups for different parts.
Read more
Workholding 5C Collet Drawbar Force Gauge
ForceCheck collet force gauges measure the drawbar pullback force of a collet workholding system. Measurement of collet drawbar force provides an easy way to ensure correct...
Hydraulic Collet Gauges
Accurate, quick and simple measuring of the clamping force of hydraulic chucks.
Wired Chuck Force Gauges (ForceCheck)
Designed to quickly check the holding force on a chuck or turning-center. The wired chuck force gauge can be customized for any diameter.
Machine-Integrated Drawbar Force Gauges (ForceCheck)
The machine-integrated drawbar force gauge automates drawbar force measurement. With a wireless force sensor stored in the tool changer, a machine can periodically automatically...
Pallet Clamping Force Gauges(ForceCheck)
Clamping force measuring gauges for pallets are intended to quickly measure the holding force of individual clamping heads.
Pallet clamping adapters are per-application...
ForceCheck Drawbar Force Carrying Cases (ForceCheck)
Depending on what gauges you need to keep together, TAC Rockford offers various carrying case configurations.
ER Collet Taper Plug Gauge Carrying Case
For holding a complete set: ER11, 16, 20, 25, 32, 40 (Gauges not included). Can be customized upon request.
Wireless Drawbar Force Gauges(ForceCheck)
The ForceCheck wireless drawbar force gauge is based on the same technology as the industry-leading ForceCheck gauge. With the added convenience of wireless operation, larger...
ForceCheck Pallet Clamping Force Gauges
For measuring the clamping and holding mechanism on various pallet-based applications
Clamping force measuring gauges for pallets are intended to quickly measure the holding force of individual clamping heads.
Pallet clamping adapters are per-application based, and are fitted according to the specifications of the customer's pallet system.
Clamping adapters can be or have been provided for various pallet systems: BERG, Rohm, Mazak, OTT, Schunk, Erowa, and others.
Clamping force measuring gauges for pallets are intended to quickly measure the holding force of individual clamping heads.
Pallet clamping adapters are per-application based, and are fitted according to the specifications of the customer's pallet system.
Complete kit can include universal ForceCheck display readout, adapter cable, pallet clamping test adapter(s), and other accessories according to pallet clamping specifications.
Pallet adapters can be or have been developed for pallet systems such as:• BERG Spanntechnik
• Rohm
• Mazak
• OTT-Jakob Spanntechnik
• Schunk
• Erowa
• And many others, whether foreign or domestic pallet clamping systems.
NAB Pull Studs (BERG)
Pull studs are the interface between devices, pallets and the clamping systems of the machine tool. For applications with two, four or more clamping heads, solid bolts are...
NSM-HV Zero Point Clamping System(BERG)
NSM-HV series zero point clamping heads are used for workholding pallet clamping as well as other applications on machine tools. With the clamping heads and matching retention...
NSM-PV Zero Point Clamping System(BERG)
NSM PV zero point clamping heads are used for fixture and pallet clamping on machine tools. With the clamping heads and the associated clamping bolts provide for the highest...
SPH Pallet Clamping Heads (BERG)
BERG Spanntechnik series SPH clamping heads are primarily used for horizontal pallet clamping. The heads form the basis of a highly rigid, high precision repeatable workholding...
SPH-V Pallet Clamping Heads (BERG)
Clamping heads of the series SPH-V are principally used in machining centers for vertical pallet clamping. The series SPH-V is based on the basic principle of the SPH. The...
SPM-HV Pallet Clamping Heads (BERG)
SPM-HV series pallet clamping heads are used for pallet clamping on single or double axis indexing tables. With the clamping heads and matching tapered rings, maximum workpiece...
Hydrodock System (BERG)
Hydrodock units form the basis of a very compact and flexible clamping system. They were originally conceptualized as for head change systems on large machining centers, but...
ForceCheck Machine-Integrated Drawbar Force Gauges
The machine-integrated drawbar force gauge automates drawbar force measurement. With a wireless force sensor stored in the tool changer, a machine can periodically automatically check the drawbar without stopping production. Drawbar force is returned to the machine control via a wireless receiver, automatically alerting the operator if insufficient force is detected.
Applications• Intended to be stored inside automatic tool changers.
• Allows for inaccessible or difficult to reach milling spindles to be tested.
• Automatic periodic drawbar force checking and reporting.
CustomizationMachine integrated drawbar force gauges are made to customer specifications, and can be fitted for any tool holder taper, size, and flange diameter. Sensors can be set to automatically trigger force readings upon insertion into spindle, and report measurements wirelessly to a console or receiver, all while using low-power consumption.
Workholding 5C Collet Drawbar Force Gauge
ForceCheck collet force gauges measure the drawbar pullback force of a collet workholding system. Measurement of collet drawbar force provides an easy way to ensure correct...
Drawbar Clamping Force Gauges(ForceCheck)
This critical performance -- the tool clamping force -- is often never measured after a machine is put into service. Regular verification allows problems to be detected early...
Kennametal (KM Taper) Drawbar Force Gauges (ForceCheck)
Measuring bars, complete sets, and base units for measuring drawbar force on a Kennametal KM spindle.
Wireless Drawbar Force Gauges(ForceCheck)
The ForceCheck wireless drawbar force gauge is based on the same technology as the industry-leading ForceCheck gauge. With the added convenience of wireless operation, larger...
Steep Taper (ISO) Drawbar Force Gauges(ForceCheck)
Measuring bars, complete sets, and base units for measuring drawbar force on a Steep Taper (SK) ISO standard spindle.
HSK Taper Wireless Force Measuring Bars(ForceCheck)
Wireless measuring adapters have the option of coming with or without the tool change groove. Wireless adapters can be retrofitted for quick inspection or designed for integrated...
Drawbar Clamping Measuring Bars(ForceCheck)
This critical performance -- the tool clamping force -- is often never measured after a machine is put into service. Regular verification allows problems to be detected early...
Capto PSK (PSC) Drawbar Force Gauges(ForceCheck)
Measuring bars, complete sets, and base units for measuring drawbar force on Coromant Capto spindles (Polygonal Shank Taper - PSK).
HSK Drawbar Sensor Position Gauges
Drawbar position gauges are used to adjust and set drawbar stroke position on HSK machine tool spindles. The gauges allow the clamping angle to be adjusted to the high and...
ForceCheck Wireless Drawbar Force Gauges
The ForceCheck wireless drawbar force gauge is based on the same technology as the industry-leading ForceCheck gauge. With the added convenience of wireless operation, larger machines and hard-to-reach spindles are easier to check. In addition, the unit offers the optional capability of data logging on a USB stick.
Item | Order Number | |||||||
---|---|---|---|---|---|---|---|---|
HSK-A/C/E 63 | HSK-B/D/F 80 | 461.320.163.000
|
||||||
HSK-A/C/E 100 | HSK-B/D/F 125 | 461.320.190.000
|
Machine-Integrated Drawbar Force Gauges (ForceCheck)
The machine-integrated drawbar force gauge automates drawbar force measurement. With a wireless force sensor stored in the tool changer, a machine can periodically automatically...
HSK Taper Wireless Force Measuring Bars(ForceCheck)
Wireless measuring adapters have the option of coming with or without the tool change groove. Wireless adapters can be retrofitted for quick inspection or designed for integrated...
Workholding 5C Collet Drawbar Force Gauge
ForceCheck collet force gauges measure the drawbar pullback force of a collet workholding system. Measurement of collet drawbar force provides an easy way to ensure correct...
HSK Taper Drawbar Force Gauges(ForceCheck)
Measuring bars, complete sets, and base sets for all HSK type spindles. Contact us for other wireless and carrying case options.
Steep Taper (MAS 403 BT) Drawbar Force Gauges (ForceCheck)
Measuring bars, complete sets, and base sets for Steep Taper (MAS 403-BT) JIS standard.
Kennametal (KM Taper) Drawbar Force Gauges (ForceCheck)
Measuring bars, complete sets, and base units for measuring drawbar force on a Kennametal KM spindle.
Wireless Sensor Operating Instructions
The ForceCheck wireless sensor measures the clamping force of power drawbars on machining centers. Designed for use with the ForceCheck Wireless Display (461.110).
<br...< p="">
Wireless Chuck Force Gauges(ForceCheck)
The ForceCheck wireless chuck force gauge is designed to quickly and accurately measure holding force and speed on chucks. Verifying chuck holding force allows manufacturers...
Steep Taper (DIN) Drawbar Force Gauges(ForceCheck)
Measuring bars, complete sets, and base sets for Steep Taper (SK) DIN standard. Metric or inch retention knob / pull-stud threading available on each measuring bar.