E-Catalog > PML-PAL Precision Air Chuck > Light Weight Precision Air Chuck
Product Information :
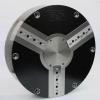
- เครื่องจักร, อุปกรณ์เกี่ยวกับเครื่องจักร, เครื่องมือกล
- PML-PAL Precision Air Chuck
- สินค้า, ผลิตภัณฑ์
Product Detail :
Light Weight Precision Air Chuck
This is a 350MM or 14" precision air chuck with three jaws and 3MM jaw stroke.
A customer approached PML-PAL engineering with a request to design a large air chuck for turning application that is going to clamp a large work piece, over 1000MM or 39". The customer asked to consider the heavy load on the spindle. He asked to design a chuck that would be as light as possible. The chuck has to be designed to hold its accuracy and repeatability for the long term as well as run at certain rpm.
Considering the light weight request, the conclusion by pml-pal was to design a chuck body made from Aluminum material that goes through anodizing process. The moving parts are inserts made of gray cast iron and inner jaws made from hardened carbon steel. The aluminum chuck weight is roughly 30kg/66lb. It is about 43% percent or 23 kg/50lb lighter than a similar chuck made of mild steel. Reapatbility is 0.006MM or 0.00024".
To read more about the manufacturing process, please review the following page.
Below is a link to an article about one of PML-PAL customer on how they retrofitted a Puma lathe
for their unique specification. Among the many changes, they mounted the above air chuck.
From the original article published on June 7th, 2013....
“It was through such discussions that we determined that our needs would be best met by
replacing the Puma’s hydraulic chuck and draw bar with a high precision, low pressure
(PML-PAL) 350mm 3-jaw pneumatic chuck system. To ensure quicker set-ups and improved
productivity a bespoke work holding system was developed using the flexible Jergens Ball-Lock
fixturing system, these are used on the modular custom chuck jaws designed and manufactured
in house by Cross".
Precision Air Chuck Body Making Process
How does a chuck get made using another high precision air chuck?
This unique case study illustrates a real situation in a machining set up where a large workpiece is machined efficiently: fast with minimum clamps. We will demonstrate how a 350mm chuck body is made using another 200mm high precision air chuck to clamp it (200-3-2.5 ST) while it is being milled.
The below large workpiece will be transformed into a chuck body using the fewest clamps possible and in the shortest time. The photos below illustrate the process along with the clamping system.
1. Large raw material waiting on the floor to be transformed into a precision air chuck body.
2. The workpiece is prepared for first operation. The bottom is milled in order to be clamped
by an air chuck from the inner diameter.
3. 200mm Stationary Precision Air Chuck with milled jaws in order to fit the above workpiece.
As noticed we are going to clamp the work piece from the inner diameter.
4. The workpiece is easily clamped on the air chuck. The gripping force is 2800kN.
5. The workpiece is milled without any obstacles around it.
6. The precision air chuck on the bottom creates obstacle free environment above and
around the workpiece.
7. This is the end of the first operation. The workpiece is done on the upper side and
outer diameter.
8. The workpiece is dismounted effortlessly and put back on the floor.
9. The next workpiece will be mounted on the chuck the same way. No need to center it
again. The repeatability is 0.002 mm.
10. Before second operation, we prepare the clamping system appropriately. The chuck
stays mounted on the machine. We remove the first operation jaws, and install another
set of jaws. Then mill them to fit the other side of the chuck body for second operation as
illustrated below. Again, clamping from the inner diameter.
11. The chuck body is then mounted instantly and ready to be machined.
12. Almost done…..
13. As noticed there are no obstacles around the chuck for smooth operation.
14. Now the second operation is done.
15. The operator dismounts the chuck body.
16. The chuck body is back on the floor.
17. As noticed, the chuck body is made from Aluminum material that goes through hard
anodizing process coated black.
We have decided to use Aluminum body in order to reduce substantial amount of load
from the overall chuck weight. The aluminum chuck weight is substantially lighter than
equivalent stainless steel chuck.
18. We used iron cast inserts and other hardened materials for the working parts
19. This is the final product from different angles.
20. The small one is a 37mm DIA mini gripper material handling precision chuck.