E-Catalog > Metrol Touch Sensors Thailand Distributors > METROL Cost reduction
Product Information :
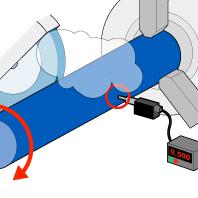
- เครื่องจักร, อุปกรณ์เกี่ยวกับเครื่องจักร, เครื่องมือกล
- Metrol Touch Sensors Thailand Distributors
- สินค้า, ผลิตภัณฑ์
Product Detail :
Cost reduction
-
Using expensive Touch Probes for Updating the wear of Grinding Stone?! Looking for more economical solution…2013.10.11
-
Contact displacement sensors used for measurement inside CNC cylindrical grinding machines cannot survive the harsh internal environment.2012.09.10
-
Radiation degrades photomicrosensors fast and we have to replace them every two or three months.2012.09.10
-
We are experiencing difficulties because the detection of double sheet metal feeding with expensive contact displacement sensors costs too much.2012.09.10
-
Radiation degrades optical fiber sensors. Are there any sensors durable under radiation exposure?2012.09.10
-
The switch is not broken but false signals frequently occurs. It is necessary to detect the opening and closing of disk brake pads without fail!2012.09.10
-
Is high-precision positioning for the driving part of equipment possible with stepper motors?2012.09.10
-
Can small-diameter drills (ø 5 mm) length detection be made more reliable? Laser sensors are prone to fail in adverse environments.2012.09.10
-
Is there any alternative to contact detection by installing an intermediate unit onto proximity sensors?
Using expensive Touch Probes for Updating the wear of Grinding Stone?! Looking for more economical solution…

Currently we are using Touch Probes for updating the wear of Grinding Stone but they cost more than 100,000 JPY per Probe, even it is a single detection of the Grinding Stone.
I am looking for contact-type sensors, as the Grinding Stone is stopped during the detection. Are there any economical sensors with the same repeatability of 1μm?
With 0.5μm repeatability at around 1/10 Price! Reducing your costs with the same specs!

Metrol Precision Positioning Switches can also be used for wear updation of Grinding Stone in CNC Grinding Machines!
Cost of around 1/10 of other Touch Probes even with the same 0.5μm repeatability!
Also, with IP67 Protective Structure for coolant and chips environment, it will contribute to reducing the cost for Grinding Stone Wear Updation!
Metrol Precision Switches have been used for detecting and updating the wear in Machining Centers and single measurement for NC Grinding machines!
Please feel free to contact us for further details!
Q&A Improvement Case Studies
We have some problems with the presence detection of wafers for semiconductor devices with photoelectric sensors.

I design semiconductor wafer delivery robots.
Currently, we use transmission photoelectric sensors to detect the presence of wafers on pickup arms. However, during the vacuum evaporation process, condensation on the viewport sometimes causes false detection. In addition, because their signal operating points cannot be viewed, it takes at least two days to mount and adjust them on site. They are troublesome and we are at our wit's end.
I read your Q&A Improvement Case Studies. I am interested in switches that can be used in a vacuum environment but I have one concern. Can contact switches damage delicate wafers?
Metrol positioning switches directly touch wafers with a low contact force of 0.5 N and special resin tips!

You might already have given up, thinking that sensors cannot be used in a vacuum.
Metrol has a vacuum-compatible precision positioning switch with a low contact force of at most 0.5 N.
In addition, the tip of the switch can be changed to special soft resin, which will not damage delicate wafers.
Metrol precision positioning switches have been introduced widely into wafer conveyors and organic electroluminescence vacuum evaporators by major semiconductor device manufacturers.
If you have any problems with the precision positioning and presence detection of semiconductor substrates and wafers, please contact Metrol.
Is there any alternative to contact detection by installing an intermediate unit onto proximity sensors?

We use proximity sensors for the detection of workpieces on the production line.
The workpieces are made from various materials such as iron and stainless steel. Therefore, we make intermediate units including non-contact proximity sensors and use them as contact type detectors, but we have concerns about their cost and mounting space. We considered the introduction of microswitches but they are not durable and cannot survive to use on the production line.
Do you have any solution for this?
Durability of 10 million operations achieved at the same price range as proximity sensors
Direct touch and considerable cost reduction!

Leave workpiece contact detection to Metrol precision positioning switches.
Metrol precision positioning switches are of the contact type.
They directly touch workpieces, so their object's materials do not matter.
The CS series have a durability of 10 million operations at a low price.
They will greatly reduce the total cost, compared with using a combination of proximity sensors and intermediate units.
Metrol also has a long stroke type (5 mm) and it will not damage workpieces by making them hit against each other.
Leave workpiece detection on the production line to Metrol.
Q&A Improvement Case Studies
Ultrasonic sensors cannot reliably detect 0.1 mm-thick sheets if the material type varies.

I improve and design offset printers dedicated for nylon sheets.
We use ultrasonic sensors for the detection of 0.1 mm-thick nylon sheets to feed them automatically when the remaining quantity drops to ten. However, they cost a lot, requiring amplifiers, and it is bothersome that the signal points vary depending on the sheet material.
Do you have any solution for 100% detection of 0.1 mm-thick sheets?
Leave it to us! We have precision positioning switches that can detect continuous displacement of 0.1 mm or thinner sheets.

Leave the detection of 0.1 mm-thick sheets to precision positioning switches.
The tip of the Metrol rotating lever-type positioning switch can be changed to a roller bearing effective to handle continuous displacement of sheets.
The switch requires no amplifiers. So, it can achieve a precision equivalent to that of ultrasonic sensors at one-third to one-half the price. As a contact-type switch, its signal point is independent of the sheet material.
In addition to offset printers, the switch has been employed to detect continuous displacement of 0.1 mm or thinner objects in seal positioning and film thickness detection that require high precision.
If you have any problems with the presence detection or position of thin sheets, please contact Metrol.
Are optical fiber sensors the best for glass substrate alignment inside vacuum film forming equipment for FPDs?

We use optical fiber sensors for the glass substrate alignment mechanism (precision positioning) used in vacuum film forming equipment for FPDs, but we have some difficulties because they require photo-irradiation via a viewport from outside the system and its processing costs are high.
I have heard Metrol switches can achieve good performance in XY stage precision positioning outside vacuum equipment. Do you have switches usable within vacuum equipment?
Leave it to us! We have precision positioning switches effective for alignment in a high vacuum.

Leave alignment inside vacuum film forming equipment for FPDs in a high vacuum to precision positioning switches.
The Metrol vacuum-compatible positioning switch is a precision mechanical device that does not use electronic elements.
It consists of low outgas components and is usable in a 10-5 Pa high vacuum.
Viewports are no longer necessary after incorporating the switch into the alignment mechanism, so considerable cost reduction is possible.
More and more major semiconductor device manufacturers have employed Metrol positioning switches for vacuum systems such as sputtering devices, evaporators and etchers.
If you have any problems with positioning in a vacuum, please contact Metrol.
Expensive sensors for spring endurance testers?
Are there any switches that can be used in automatic stop mechanisms?

I engage in the manufacture of compact precision springs for transport planes.
During the spring endurance test, we use a dedicated endurance tester. We are now considering a mechanism to stop the tester automatically whenever a spring breaks.
I consulted a sensor manufacturer and they recommended a method to detect breakage by permanently irradiating springs with a photoelectric sensor. However, it is too expensive for a tester...
Do you have any better ideas with simple ON/OFF switching?
Leave it to us! We have precision positioning switches capable of detection with not only high-precision but also simple ON/OFF signals.

Leave simple ON/OFF signal output to precision positioning switches.
How about the mechanism illustrated above?
1) In the normal state: The switch is ON because of spring tension.
2) At breakage: The switch turns off when the spring tension is lost.
You might think precision positioning switches are also expensive but their mechanism is simple and the cost per switch is not so high.
Please try contacting Metrol.
Q&A Improvement Case Studies
The intermediate mechanism installed for the detection of screws in pinholes with a proximity sensor costs too much.

We use proximity sensors to detect the presence of screws in pinholes, but they require intermediate actuators to function. We are experiencing difficulties because this not only enlarges the system but also increases the total cost.
Do you have any solution for this?
Leave it to us! Deep-base holes, narrow shoulders and protrusions. We have positioning switches capable of detecting objects having unusual shapes that proximity sensors can not.

Leave special shape detection such as deep-base holes, narrow shoulders and protrusions to precision positioning switches.
Proximity sensors and photosensors cannot detect objects in pinholes unaided and, generally, it is necessary to activate sensors via intermediate mechanisms.
However, the point (contact) of the Metrol CS series precision positioning switch can be customized according to the dimension and shape of the object to be detected, which enables the detection of screws in pinholes with direct contact.
Q&A Improvement Case Studies
Are expensive touch probes necessary in end face measurement for grinders?

Currently, we use touch probes from a measuring equipment manufacturer for the measurement of the cutting allowance of ingots and their after-process inspection. However, we are experiencing difficulties because, in spite of the simplicity of the measurement, the probes are very expensive.
Now, one of our client companies intends to expand its equipment and we have received a request to reduce the cost. Do you have any sensors that can achieve the same 1 μm repeatability at a lower price?
We have precision positioning switches that can achieve 1 μm repeatability at half the cost. Leave end face measurement for NC grinding machines to precision positioning switches.

Leave end face measurement for grinders (NC grinding machines) to precision positioning switches.
The Metrol touch probe for NC grinding machines can achieve 1 μm repeatability in ingot end face measurement at a low price.
(This has become possible because Metrol specializes in precision positioning switches.)
More and more major machine tool manufacturers have employed Metrol precision positioning switches for workpiece detection in NC grinding machines and machining centers.
If you have any problems with end face measurement and workpiece detection in NC grinding machines, please contact Metrol.
Q&A Improvement Case Studies
We are experiencing problems with connectors for optical fiber sensors inside vacuum film forming equipment.

Currently, we use vacuum-resistant optical fiber sensors in the precision positioning of glass substrates inside vacuum film forming equipment for organic electroluminescent panels. But wiring cables for sensors outside the evaporation chamber requires dedicated connectors and they are very expensive.
What can we do without those expensive connectors in precise positioning in a vacuum environment?
Leave it to us! We have precision positioning switches effective in a high vacuum environment.

Do you think that mechanical switches are unsuitable for use in a vacuum environment?
The Metrol high vacuum-compatible precision positioning switch is a precision mechanical device, consisting of only low outgas components. It can be used in a 10-5 Pa high vacuum.
Because low-cost general vacuum-compatible connectors can be used for the switch, the cost for wiring outside the system can be reduced considerably.
In addition to high vacuum environments, positioning switches have been used under radiation exposure and in magnetic fields.
If you have any problems with precision positioning semiconductor glass substrates, please contact Metrol.
Q&A Improvement Case Studies
Can 1 mm or smaller slight movements of diaphragms be detected stably with switches?

Currently, we use microswitches and proximity sensors for diaphragm valve opening/closing confirmation but it seems they cannot stably detect minor movements of the internal valve opening/closing mechanism (1 mm or smaller).
I want to improve the reliability of detection at minimum costs. Do you have any good solution for this?
Even 0.1 mm-scale slight movements can be detected without fail. The use of precision positioning switches is the solution!

Microswitches and proximity sensors have a dead band between on and off states (i.e., hysteresis). Therefore, they are actually not suitable for the detection of slight movements.
We must say that, in particular, it is very difficult for them to detect 1 mm or smaller movements.
In fact, many people experience this problem, being forced to construct mechanisms to magnify slight movements or having to consume excessive time for mounting and adjustment of microswitches and proximity sensors.
In contrast, Metrol precision positioning switches do not require amplifiers, consisting of precision components. So, free of hysteresis, they can detect 1 mm or smaller slight movements without fail.
Their reliability has been proved and a considerable number of them have been used in the disk brakes of elevators that have very stringent safety requirements for their pad opening/closing confirmation (merely 0.5 mm slight movements).
Q&A Improvement Case Studies
We need to correct the deviation of printing plates in micron increments.

I design business rotary presses.
I am experiencing difficulties because all the CMYK-color drums deviate by a few microns during printing.
Even a slight deviation can greatly affect the quality of print, so it is necessary to control drum positions precisely but optical fiber sensors are not good enough in accuracy.
I consulted some manufacturers and they recommended expensive contact displacement sensors. However, considering the mounting space and costs, we didn't employ them.
Do you have any solution for this?
Leave precise drum positioning impossible with optical fiber sensors to Metrol precision positioning switches!

Leave the positioning of printer drums to Metrol.
Optical fiber sensors are so-called presence detection sensors and they are not suitable for positioning that requires high precision.
However, there is no need to give up!
Metrol positioning switches achieve 1 μm repeatability at a lower price than that of optical sensors and correct deviations of printing plates with high precision.
Metrol positioning switches have been introduced widely in the printing industry that requires high quality in double-feed detection and paper remaining quantity detection.
Can small-diameter drills (ø 5 mm) length detection be made more reliable?
Laser sensors are prone to fail in adverse environments.

I engage in the manufacture of drilling machines for printed circuit boards using small drills having a diameter of 0.5 mm.
Currently, we use expensive laser sensors to detect the length of small-diameter drills but we are experiencing difficulties because they frequently malfunction because of scattering chips and dust from dry machining.
If possible, we want to conduct more reliable detection with the same precision (1 µm repeatability) as laser sensors, but the diameter of the drills is as fine as 0.5 mm and I wonder if contact-type devices may break them.
Are contact-type precision positioning switches effective in the detection of the length of small-diameter drills (ø 0.5 mm) ?
Contact-type sensor immune from harsh environments
positioning switches precisely detect the length of drills having a diameter as small as 0.5 mm with a low contact force of 0.5 N.

Using the low contact force type precision positioning switch with 0.5 N contact force, it can detect the length of drills having a small diameter of 0.5 mm.
The normal operation mode is closed, and the pre-travel (distance before starting operation) is almost 0 mm. That is, the switch transmits position signals the moment when it makes contact with an object, which keeps the force on drills to a bare minimum.
In addition, contact switches are less likely to cause malfunction because of adverse environmental conditions such as scattering chips and dust and can achieve a precision overwhelming that of laser sensors (0.5 µm repeatability) at low cost.
Metrol has occupied the world No. 1 share of switches in the field of small-diameter drill length detection and zero seek of small machining centers including printed circuit board processors and tapping machines.
Q&A Improvement Case Studies
The switch is not broken but false signals frequently occurs. It is necessary to detect the opening and closing of disk brake pads without fail!

I design disk brakes for elevators.
To confirm the opening and closing of the brake pad, we install a lever-like mechanism to magnify the movements of the pad and detect those movements with microswitches and proximity sensors. However, the movements are too minor (0.5 mm) to detect stably.
This system is very important because false detection may lead to accidents, and we need to increase the reliability of detection. Do you have any solution for this?
Even slight movements as small as 0.5 mm can be detected without fail! The use of precision positioning switches is the solution.

Microswitches and proximity sensors have a dead band between on and off states (i.e., hysteresis). Therefore, it is very difficult for them to stably detect 0.5 mm slight movements.
In fact, many people experience this problem, being forced to construct mechanisms to magnify slight movements or having to consume excessive time for mounting and adjustment of microswitches and proximity sensors.
However, there is no need to give up!
Metrol precision positioning switches are precision mechanical devices. They consist of precision components and are free of hysteresis. So, they can detect slight movements as small as 0.1 mm without fail by directly touching the brake pad.
Q&A Improvement Case Studies
Radiation degrades optical fiber sensors.
Are there any sensors durable under radiation exposure?

We use a materials structural analysis system to analyze molecular structures with radiation.
Inside the system, for the positioning of a slit to narrow the radiation (e.g., neutron) beam, we use an optical fiber sensor. However, we have concerns about it because radiation shortens the life of the sensor.
Are there any good methods for high-precision positioning even under radiation exposure?
You might already have given up using sensors under radiation exposure.

As you indicated, radiation degrades most types of electric materials such as electronic components and printed circuit boards. However, there is no need to give up, thinking electric sensors cannot avoid such damage.
The Metrol radiation-compatible precision positioning switch is of the precision mechanical type, consisting of radiation-resistant components. They do not include electronic components, so they are not damaged by radiation.
In addition to radiation environments, we have experience of precision positioning switches used in a high vacuum or magnetic fields.
If you have any problems with positioning in special environments, please consult Metrol.
We are experiencing difficulties because the detection of double sheet metal feeding with expensive contact displacement sensors costs too much.

I engage in 0.5 mm-thick sheet metal working on spot welding lines. Although they happen very rarely, when feeding sheet metal on the line, double-feed errors do occur and these cause defective products.
Currently, to prevent this, we use contact displacement sensors with a repeatability of 1 μm and make them display the thickness to assess whether the number of fed sheets is one or more (if the thickness is greater than 0.5 mm, it is assessed as an error).
In this way, defective products have been prevented, but we have a problem because those sensors are too expensive.
Do you have any better solution?
Cost reduction, achieving the same precision as contact displacement sensors!

Is value indication really necessary in the detection of sheet metal double feeding?
Contact displacement sensors with a display unit may be an over-engineered solution for positioning on automated lines.
Metrol precision positioning switches can achieve as high precision as contact displacement sensors at a low price without requiring expensive amplifiers.
High repeatability of 1 μm is achieved at a low price. With precision positioning switches, double feed detection of sheet metals with a combined thickness of only 0.7 mm can easily be done.
Please reconsider if value indication is really necessary for positioning on automated lines.
Q&A Improvement Case Studies
Radiation degrades photomicrosensors fast and we have to replace them every two or three months.

I design molecular accelerators used in a large-scale synchrotron radiation facility.
We use photomicrosensors in the positioning of a slit to narrow neutron beams. Sensors cannot be used inside the system because they are affected by radiation, so an intermediate mechanism is installed outside the system for detection.
However, we are experiencing difficulties with the following issues:
1) Sensors deteriorate because of slight radiation even outside the system and they need replacing every two or three months.
2) The precision of detection is naturally low because the detection is made via the intermediate mechanism.
3) The intermediate mechanism makes the system larger.
Are there any methods to position the slit with high precision even under radiation?
Leave precision positioning under radiation to precision positioning switches.

Leave positioning under radiation to precision positioning switches.
The Metrol radiation-compatible precision positioning switches are of the precision mechanical type made with materials that can be used under radiation. They do not include electronic components, so they are not damaged by radiation.
By incorporating the switches into the system and making them touch the slit directly, the following can be realized.
1) Elimination of labor required for replacement and repair, because the switches are immune from radiation
2) Repeatability of 1 μm
3) Size and cost reduction of the system requiring no intermediate mechanism
In addition to radiation environments, we have experience of precision positioning switches used in a high vacuum or magnetic fields.
If you have any problems with positioning in special environments, please consult Metrol.
Q&A Improvement Case Studies
Contact displacement sensors used for measurement inside CNC cylindrical grinding machines cannot survive the harsh internal environment.

I design machines dedicated to semiconductor manufacturing (CNC cylindrical grinding machines).
We use contact displacement sensors with a value display function to measure the outer diameters of ingots before and after grinding.
The measured values are then fed back to the equipment for after-process inspection. However, we are experiencing difficulties because sensors are affected by coolant, scattering chips and dust inside the grinding machine and that causes malfunction.
In addition, the required display unit is costly.
To achieve 1 μm-precision measurements in adverse environments, contact-type devices are necessary. Do you have any solution for this?
Is value indication really necessary? Leave ON/OFF position signals to the digital scale of the equipment.

Leave outer diameter measurement for workpieces inside CNC cylindrical grinding machines to Metrol.
Are displacement sensors with a value display function really necessary for the outer diameter measurement for ingots inside machine tools?
The Metrol touch probe-type precision positioning switch is designed exclusively for machine tools.
By measuring high-precision ON/OFF position signals with a digital scale of the equipment, the outer diameter of ingots can be measured without using a value display unit.
In addition, the touch probe-type precision positioning switch is immune from coolant, scattering chips and dust and can achieve 1 μm repeatability in such adverse environments.
It has been introduced widely for inner and outer diameter measurement and the centering of workpieces by major machine tool manufacturers.
Please try contacting Metrol about its precision positioning switches.